Developing Integrated Solutions in an Evolving Hydrogen Market
- NanoScent Labs
- Oct 12, 2023
- 6 min read


Introduction
Across the hydrogen value chain, there are many points where integrated solutions play a crucial role, from production to HRS infrastructure.
From dedicated high pressure cylinders, to industrial applications that combine multiple systems for efficient on-site utilization and distribution, from tailoring the right quality measures to taking into account safety control… Integrated solutions are a part of every step of the way, from when the hydrogen is first made to when it reaches the end-users.
Challenge of a New Market
However, one of the biggest challenges for integrated solutions (which by design need to perfectly fit the market needs) is to be able to develop and make strategic decisions for product development in a market that is not yet stable and mature.
While a lot of efforts are being made to push hydrogen forward as a reliable source of energy, there are still many unknowns and this ultimately affects integrated solutions across the value chain.
For example, what type of production method will be dominating the market? SMR is currently the source of over 95% of hydrogen produced, but the goal is to make electrolyzers the top method of production in order to reach climate-neutral targets. Or, another example, what kind of distribution method will predominate the market? Tube trailers? Pipelines? On-site?
Due to the unknowns that characterize the direction of hydrogen as a market, this places an extra strain or challenge on integrated solutions developers. Furthermore, the majority of projects are not yet operational and are either in the design phase or are being built. For example, many large projects are currently underway around the world, such as NEOM for which integrated solutions are definitely a must-have. However, without operating at such a large scale and receiving customer feedback before, time for improvements gets set back.

Now, we will take a closer look specifically at how three examples of integrated solutions are developing across the value chain. The selected examples include:
cylinders
compressors, as well as
sensors where we will share our own experience about developing in an evolving market.
Example 1: Cylinders

Some of the major challenges that cylinders as an integrated must address as an integrated solution revolve around the following:
Complying with safety requirements that come along with working with high pressure and maintaining pure and clean hydrogen.
Maintaining competitive costs through manufacturing, and essentially not creating additional costs for the user due to storage.
Identifying market needs; for example, one priority from the market is to use lighter materials that puts less of a strain on transportation.
Adhering to strict requirements for hydrogen quality.
Advancements of Cylinders
With regards to innovation, we have seen some big highlights recently, including adding more advanced and complex data and communication systems to the cylinders.
With regards to design, the US Department of Energy’s Hydrogen Program, declared an initiative for innovative cylinder design in order to reduce the costs associated with the manufacturing process, but even then 72% of the cost is still attributed to the cylinder materials suited for high pressure.
It is clear that each of these improvements requires commitment for a long route of development that is determined by the market needs and affected by decisions that are yet to be made.
For example, if the market will choose liquid hydrogen over gaseous then major structural changes will be required, or, if the majority of hydrogen distribution will be done via pipelines then again the requirements for the cylinders will need to be re-defined and cylinder companies will subsequently be affected by shifting market demands.
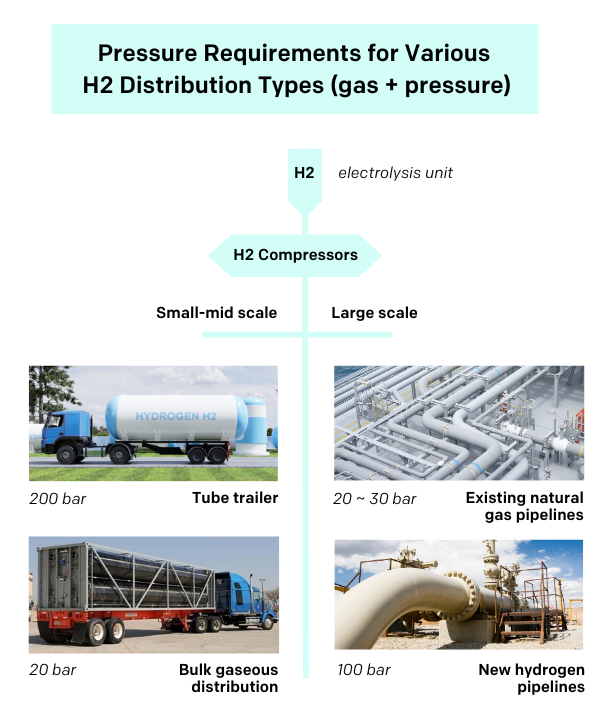
Example 2: Compressors
Compressors face challenges that relate to hydrogen’s volatile nature as a gas and high reactivity, along with the specific requirements of the hydrogen supply chain.
These compressor-related challenges include:
material compatibility because hydrogen can cause embrittlement and leakages in certain materials,
furthermore, certain compressors can introduce impurities to the supply
Another challenge is related to the required high pressures and efficiency

One way that the extent of the challenges compressors face can be seen when considering how they are being used to compress hydrogen for large-scale storage.
In this case, there are essentially two types of compressors that are suitable for this feat, which are: centrifugal compressors and also reciprocating compressors, also known as piston-type compressors. Let’s consider how these two types of compressors are developing in the market.
As governments are playing a significant role in moving the hydrogen market ahead, some bodies like the US DOE have set targets for both types of compressors for large-scale storage. Several companies have taken these targets and have even stated publicly that they want to surpass them.

In parallel to this, new compressor technologies are also emerging, such as LMRC compressors and compressors that can handle hybrid H2 blends.
When a buyer is seeking to invest in a compressor, multiple factors impact the decision-making process. Thus, while there are development targets and emerging technologies appearing, it is difficult to pinpoint on which will dominate the market from a business perspective.
Hydrogen Quality Impacts Integrated Solutions
Across the examples we have mentioned so far, hydrogen quality plays a crucial role.
For example, with cylinders, it is vital to ensure that there are no contaminations leaking in, and with compressors it is crucial to validate that no contaminations are introduced into the vacuum. So hydrogen quality is a common theme for these two integrated solutions that also affects their performance and impact across the value chain.
Hydrogen quality is important because in order for hydrogen to be used as a fuel and gas it must be clean and pure.
Contaminants are considered to be any molecules that are not hydrogen, such as nitrogen, humidity, carbon monoxide, sulfur, and oxygen. Each contaminant has a different effect, while some are just diluting the hydrogen, like nitrogen, some may cause reversible and irreversible damage.
There are industry standards that define purity levels according to the concentration of hydrogen and the permissible levels of contaminants as expressed in ppm or ppb levels.
Example 3: NanoScent Sensors

In the final example, sensors are discussed as a type of integrated solution that are being challenged by the evolving market.
I will share first-hand how we tackled these unknowns and developed a product strategy around it, in order to start monitoring hydrogen quality in real-time for multiple stakeholders in the supply chain.
We understood that the position we need to take in order to advance in the changing market is to set the standards! We are working closely with metrology institutes around the world and with experts in hydrogen production and supply to set the standard of monitoring the quality of the hydrogen.

As mentioned previously, there are different points of the hydrogen value chain where monitoring hydrogen quality is relevant, from electrolyzers to HRSs, to compressors and various hydrogen carriers like LOHC.
As a startup, we prioritized hydrogen production because everything else revolves around its supply. So we see that as hydrogen production grows, which is estimated to reach 530Mt by 2050, other segments of the value chain will grow as well.
HRS stations will become more abundant, compressors will need to work more for mass-scale storage, and eventually new technologies like LOHCs will follow.
We noticed that across each of these different parts of the value chain, there are different needs and contaminants of interest when it comes to monitoring hydrogen quality. Thus, we concluded that for development, a modular approach would be best - allowing customers to choose essentially what contaminants they want to monitor while keeping the mechanical and electrical elements identical.

So what does this mean? I will give a few examples.
With regards to electrolyzers, humidity and oxygen are the biggest contaminants of interest since it only uses water and air to produce hydrogen. Furthermore, with regards to safety, O2/H2 Crossover is really important to take into account.
For compressors, Oily VOCs can be introduced into the supply and for LOHC and hydrogen carriers, aromatics and ketones are relevant.
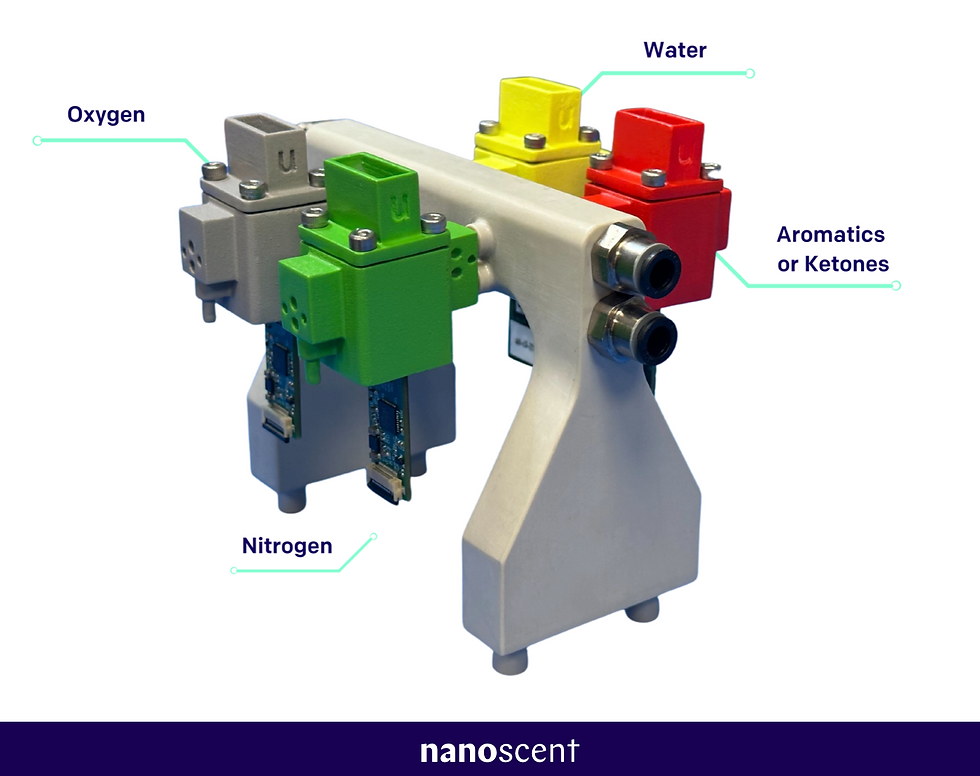
To be able to address multiple requirements from various users in the value chain, Nanoscent has taken the modular approach, this means that the product used to monitor the quality of the hydrogen is tailor made for the customers needs.
For example, customers that are using hydrogen that is directly produced from an electrolyzer, may only want to monitor oxygen and moisture, for them we have the same product VOCID® H2Confirm with two modules for oxygen and for humidity.
Other customers, who use hydrogen from ammonia cracker, may want to monitor ammonia and for them we can offer another module for ammonia traces in hydrogen.
Below, you can see how we also made the integration very simple, almost like plug and play. You only need to connect two inlets, one for sample and one for reference and have one outlet connected to the customers vent system. H2Confirm is made to be simple and easily handled and operated.

Here, you can see the specification of our first product used to monitor moisture levels in hydrogen:

So, this is our approach for working in an evolving market, to do it in a modular way and step by step, this is beneficial both for RND and for the customers!
For more information, please contact us.
Comments